Success Story: SONOTEC X PD Energy GmbH
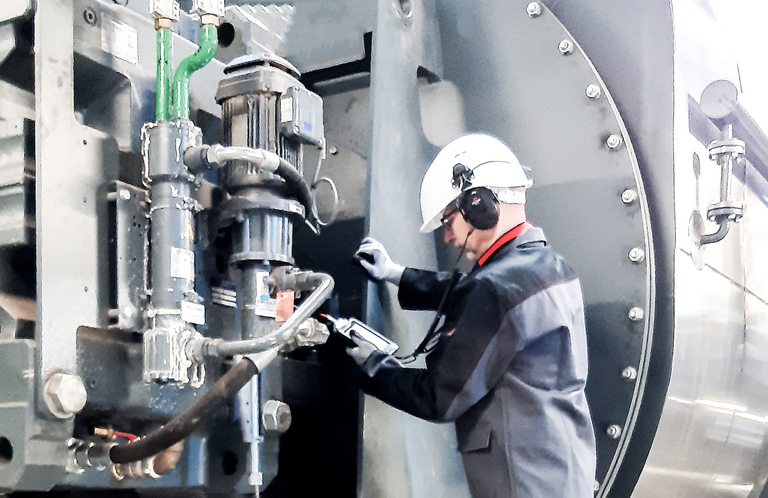
Ultrasound is the technology for the first step in damage detection and has the advantage over other methods in that it can be used at all bearing speeds. Even with extremely low-speed bearings, damage can be detected at the earliest possible stage.
“Low-speed machines like our sewage sludge dryer are difficult to monitor with vibration measurement technology. With SONOTEC's ultrasonic technology, it was possible to detect roller bearing damage and assess its condition," says Tobby Brümmer, Head of Machinery Maintenance at PD Energy GmbH
Focus on sewage sludge incineration
As a 100% subsidiary of PD energy GmbH, KSR sewage sludge recycling Bitterfeld-Wolfen GmbH operates a mono sewage sludge incineration plant in the Bitterfeld-Wolfen chemical park. The plant is designed for a rated thermal output of 19.9 MWth. Running more than 8,000 hours a year, the incinerator consumes up to 260,000 tons of dewatered sewage sludge from municipal sewage treatment plants. The thermal utilization of sewage sludge in mono-incineration plants will be an important disposal path in the future. With the construction of the plant, KSR sewage sludge recycling Bitterfeld-Wolfen GmbH is making a contribution to the phosphorus recovery that will be required in Germany starting in 2029. The finite resource is filtered out via various systems and fed back into the material cycle.
Slow-speed disc dryer
The core process in the treatment of sewage sludge is drying. Two disc dryers are used at the site for this purpose. The redundancy of the systems is important so that one dryer can always process sewage sludge. However, the system capacity is designed in such a way that both dryers are always running, if possible, in order to be able to achieve the appropriate utilization. Downtimes must be kept as short as possible, and if they are necessary, they should only affect one dryer at a time. "The availability of both disc dryers is extremely important to us," says Tobby Brümmer, Head of Machinery Maintenance at PD Energy GmbH. In the disc dryer, the material is slowly transported from one end to the other, reducing the residual moisture. Disks heated with steam form a large contact surface where indirect drying takes place. Scrapers ensure an even process and transport of the material. The rotor turns very slowly with only 7.5 revolutions per minute.
Roller bearing damage detected and evaluated
During the commissioning phase, noises were detected on a roller bearing on one of the two dryers, whereupon a vibration measurement was initiated. “The results of the vibration measurement were not useful for us. They showed no indication of damage to the examined roller bearing,” says Tobby Brümmer. After a short research it was clear that ultrasonic measurement technology could help. "We then contacted SONOTEC GmbH and asked for a measurement using ultrasonic technology," adds Tobby Brümmer. During the on-site measurement, the damage could be narrowed down to the corresponding roller bearing. The measurement effect was clear and in comparison to the second dryer, a statement about the severity of the damage could be made on-site. The subsequent evaluation by the application engineer from SONOTEC provided further insights. It could be confirmed that the damage to the roller bearing had to be severe and very advanced. Furthermore, the data analysis revealed that the outer ring must have been severely damaged and, in particular, that one race of the double-row bearing was more severely affected. “Such details are extremely important for us to be able to identify the causes as precisely as possible. This is the only way to take appropriate preventive measures to prevent the problem from reoccurring,” says Tobby Brümmer.
Solution for slow-movers: condition monitoring with ultrasound
The advantages of ultrasonic testing technology from SONOTEC are very apparent in this application. The broadband data evaluation enables an optimal adjustment to the conditions on site. In this way, characteristic values can be calculated in the range from 20 kHz to 128 kHz. Frequency ranges with background noise can be suppressed with the adjustable filter function. The high sensitivity of the sensors enables early detection of roller bearing damage, making ultrasonic monitoring a very effective solution, especially for slow-running roller bearings. “We are excited about the statements that can be made with the help of the ultrasound data. Ultrasonic roller bearing monitoring will be an integral part of our maintenance measures for our slow-moving machines in the future,” explains Tobby Brümmer.
SONAPHONE: A modular approach with different apps and sensors
With the ultrasonic testing technology from SONOTEC, other applications in preventive maintenance can also be performed. The device makes it possible to locate and evaluate compressed air leaks, and steam traps can be tested and their condition evaluated. Both applications are moving more and more into the focus of many companies due to ever increasing energy costs. "We are also interested in the other possible applications of ultrasonic technology," says Tobby Brümmer. With various apps and corresponding sensors, the ultrasonic testing device SONAPHONE can be easily adapted to the respective application. “This means that the investment in the testing equipment pays for itself very quickly. And the device is better utilized by using it in different departments. It is used between the regular routes on the disk dryers for other applications," says Tobby Brümmer.
Interview partner: PD energy, Tobby Brümmer, Head of maintenance for machine technology