Liquid Flow Meter Measurement Principles
Advantages and Limitations
The market for flow meters is continuously growing. The specialized sensors are applied in more and more processes to increase reliability and efficiency. What do researchers need to look for when deciding which kind of flow meter with which measurement principle to use?
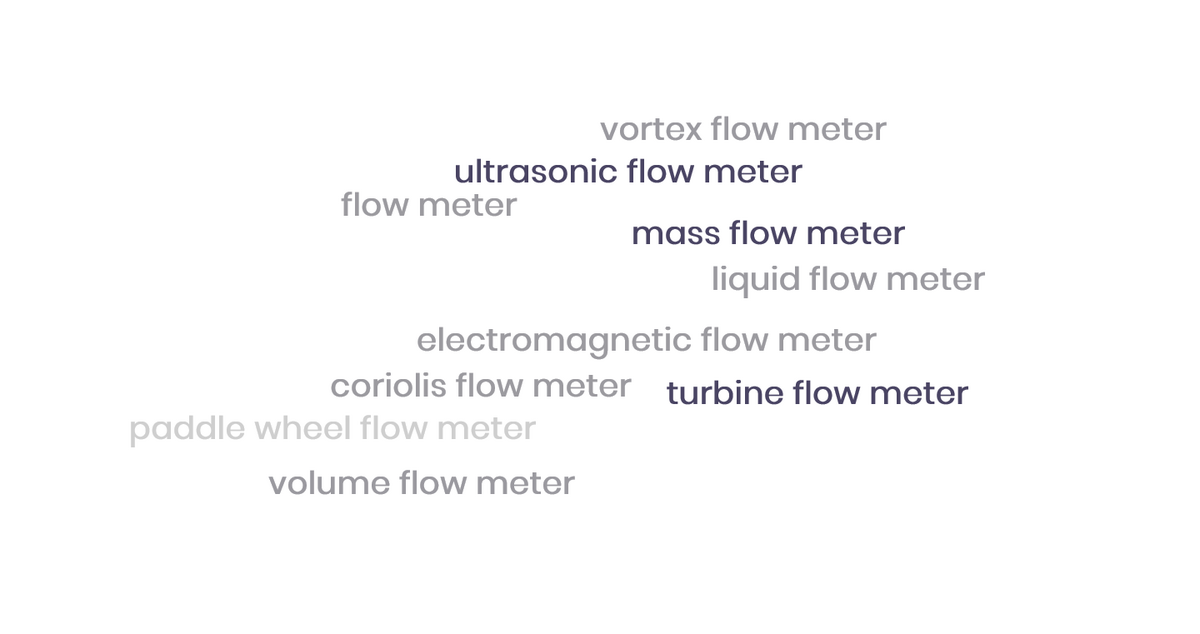
Accuracy & Repeatability: Key for Measurement Principles
Depending on the measurement principle, manufacturers offer two general types of sensors: sensors measuring the flow with direct contact to the media, and sensors that measure without any contact to the media. Direct contact with the media implies regular cleaning of the sensor, which is time-consuming and expensive. Even when disposable single-use sensors are implemented, the replacement is similarly time-consuming as well as expensive in the long run. Sustainable sensors without contact to the media are also called non-contact clamp-on sensors as they are clamped on the tubing and measure through the tubing wall.
Flow measurement is a complex topic for process engineers: They must decide which measurement method fits best to the process and at which point the flow measurement should be implemented. Additionally, the flow profile and the characteristic of the liquid are also important for the decision about the measurement device. Viscosity, temperature, pressure, presence and amount of particles, the sensitivity of cells and the purity of the liquid are only a few more questions, which should be discussed in the buying decision.
Considering flow as a critical process parameter (CPP) in bioprocessing, flow measurement becomes even more important in quality by design (QbD) strategies in the development and production of biopharmaceuticals. Particularly, reproducibility is a key factor to achieve a constant high product quality.
Thus, accuracy at low and high flow rates is one of the top requirements for flow meters in bioprocessing.
The operator’s side is also an important factor, which covers usability including process implementation, calibration and cleaning issues, as well as pricing and the sustainability of the flow meter. Considering all those points, a certain measurement principle can make the difference.
Physical Background
In general, flow measurement is the quantification of the movement of fluids. The flow can be indicated in several ways such as velocity, flow volume or mass flow rate. The flow volume is typically specified in millilitre or litre per period, whereas the mass flow volume is given in grams or kilograms per period.
In order to measure the flow, volume counters or flow meters are used.
Despite their similarity, the terms ‘counter’ and ‘flow meter’ do not refer to the same thing: ‘Counting’ describes the recording of a quantity without any reference to a period of time, whereas ‘measuring’ defines the recording of the quantity per a defined period of time. Thus, for example, volume counters indicate litres, whereas flow meters measure in millilitres per minute.
For counting the flow volume a number of devices, such as a turbine flow meter, paddle wheel flow meter and vortex flow meters are available.
For measuring the flow volume, volume and mass flow meters are used such as electromagnetic flow meters, Coriolis flow meter, and ultrasonic flow meters.
All measurement devices, counters and flow meters, are influenced by certain ambient conditions as well as the characteristic of the liquid. So far, there is no ready-to-use solution on the market. The measurement device must fit to the application and the environment.
Advantages & Limitations of Typical Measurement Principles
Turbine Flow Meters and Paddle Wheel Flow Meters
Volume counters convert the mechanical action of the turbine or paddle wheel, which is rotating in the liquid flow, into a flow rate. The partial volume is known, which is separated through the turbine or paddle wheel. The rotational speed is proportional to the fluid velocity.
Benefits
- Usable at extreme temperature and pressure
- Little to no energy costs
Limitations
- Not suitable for low flow rates or sensitive cell suspensions
- Only for liquids with low viscosity
- Moving parts
- Cleaning issues
- Inline measurement with direct contact to the media
Vortex Flow Meters
For this measurement method, obstacles are placed in the path of the fluid. While the fluid passes the obstacles, disturbances are caused. By means of the Kármán vortex street principle, the flow volume can be determined.
Benefits
- Robust device without moving parts
- Independent of temperature, pressure and density
Limitations
- In-line measurement with direct contact to the media
- Disturbance may affect cell suspensions
- Cleaning issues
Electromagnetic Flow Meters
The sensors use a measurement method based on Faraday's law of electromagnetic induction. The flow meter measures the liquid flow by the voltage induced across the liquid via its flow through a magnetic field. The electromagnetic flow meter requires a conducting fluid.
Benefits
- Independent of temperature, pressure, density, viscosity and concentration
- Low maintenance
- Adjustable measurement range
- Independent of soiling and sedimentation
Limitations
- Fluid must be conductive
- Susceptible to error in presence of gaseous components in the liquid
- In-line measurement with direct contact to the media
Coriolis Flow Meters
Coriolis flow meters can also be called mass flow meters. The device measures the mass flow rate of the liquid passing through a tubing. These mass flow meters measure the frequency of the vibrations caused by a moving liquid that passes through a curved metal measurement pipe. The measurement principle is based on the Coriolis effect.
Benefits
- Very precise measurement of low and high flow rates
- Additional measurement of temperature and density
- Independent of changing temperature, pressure and viscosity
- Adjustable measurement range for flow and density
Limitations
- Dimensions of the sensor housing
- In-line measurement with direct contact to the media
- Sensitive to vibrations caused by improper mounting
- Susceptible to error in presence of gaseous components in the liquid
- Cleaning issues
- Very high price
Ultrasonic Transit-Time Flow Meters and Doppler Flow Meters
For the transit-time method, the sensor measures the time of flight of the ultrasonic wave with and against the streaming liquid. The time difference between both signals is a measure of the velocity of the streaming liquid. The fluid velocity and known area of the measurement channel are related to the specific volume flow.
Ultrasonic Doppler flow meters measure the Doppler shift resulting from the reflection of the ultrasonic beam from the particulates in the liquid. The frequency of the transmitted beam is affected by the movement of the particles. This frequency shift can be used to calculate the fluid velocity.
Ultrasonic flow meters can be clamped on the tubing to measure through the tubing wall without any contact to the liquid. Additionally, there are also inline ultrasonic flow meters on the market, which measure the flow velocity with direct contact to the media, which implies regular cleaning comparable with the previously discussed measurement principles.
Benefits
- Very precise measurement of low and high flow rates
- Very responsive with lowest response time
- Clamp-on flow meters without contact to the media
- Sustainable as reusable
- No moving parts
- Doppler measurement suitable for flow measurement in liquids with solid material
- No maintenance needed for clamp-on flow meters
Limitations
- Transit time principle not suitable for liquids with solid material
- Cleaning issues only for in-line measurement
Clamp-On Sensors
Single-Use vs. Reusable Flow Meters
As the demand for single-use material increases, the market for single-use flow meters is also rapidly growing. Today, for all the previous-mentioned measurement methods, single-use sensors are available, which are implemented in the process by using standard connectors with direct contact to the media. Depending on the complexity of the measurement method, certain types of single-use flow meters can be quite price-intensive considering they are used only once. Although single-use sensors are not designed to be cleaned, the high price of some sensors may tempt operators to perform one or more cleaning cycles.
Single-use implies fast implementation and usability, but the reality shows that single-use flow meters require much more effort than reusable clamp-on sensors in terms of process design, logistics, warehousing and sustainability.
Additionally, due to their reduced design, housing and lower price, single-use flow meters usually do not offer the same high accuracy and repeatability readings as reusable sensors.
In-line Measurement and Cleaning Issues
Except for the clamp-on ultrasound flow meters, all other sensors measure in-line and thus with direct contact to the liquid. Consequently, these flow sensors must be professionally cleaned on a regular basis, which is time- and cost-intensive. Depending on the design of the measurement channel, the cleaning procedure can be very complex. In general, it can be assumed that the simpler the setup of the measuring channel, the more efficiently the cleaning can be performed. However, there is always possible adhesion in the flow path inside of the flow meter. Generally speaking, this means that sensors without any moving parts in the measurement channel are more suitable for sensitive bioprocesses. By implementing single-use in-line sensors that are replaced after each cycle, contamination can be reduced to a minimum.
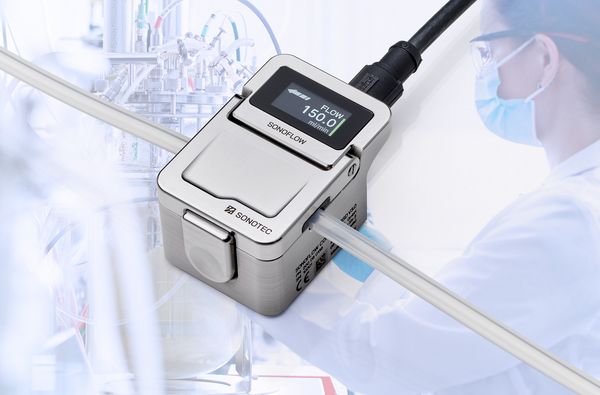
Stainless Steel Flow Meters
In order to avoid any surface contamination in GMP environments, flow meters with stainless steel housings are a viable option.
Stainless steel clamp-on ultrasound flow meters combine a number of advantages regarding cleaning and non-contact measurement in PAT-compliant bioprocessing.
Conclusion
As there is not a measurement technology that meets the requirements for all processes at the same time, the application is the key to select a suitable flow meter. Assuming that in bioprocessing, accuracy and repeatability are of the highest priority, certain measurement methods are more in focus, ie, Coriolis, electromagnetic and ultrasound. Once calibrated, if necessary, these measurement principles can achieve an accuracy of 1% and better. Disposable single-use sensors commonly have higher deviations due to their design and usage.
Where there are benefits, limitations are also not far away: the high accuracy of the reusable sensors is mostly related with a higher purchase price. Therefore, it is also necessary to evaluate follow-up costs, which refer to cleaning, supply chain management for single-use procurement and warehousing, as well as service and recalibration.
The application is key to select a suitable flow meter.
However, it is not a secret that Coriolis mass flow meters offer the most precise measurement and are not influenced by changing fluid characteristics, but there are also limitations concerning usability. Ultrasonic non-contact clamp-on flow meters can be an ideal device for single-use environments as the tubing skids can be conveniently replaced and the cleaning of the sensor can be reduced to its surface in GMP applications.
Finally, it is always a matter of weighing up the benefits and limitations of the measurement method for the respective application. There is no perfect solution on the market. Focusing on the most critical requirements in the specific process is the key to select the most suitable flow meter.
Do you have any questions?
Feel free to contact us! We will be happy to help you.
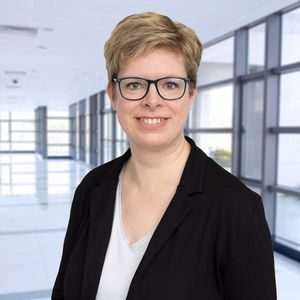