Maintenance of Compressed Air Systems | apikal GmbH
Leak Detection and Evaluation with the Ultrasonic Testing Device SONAPHONE®
Compressed air systems are still the biggest energy consumers in the industry. Apikal Anlagenbau GmbH has focused on innovative and energy-efficient solutions specialized in compressed air technology. The compressed air specialist has recently become a maintenance specialist supported by innovative technology from SONOTEC. The Ultrasound test device SONAPHONE can detect leaks in compressed air systems and automatically evaluate them. A real innovation - Made in Germany.
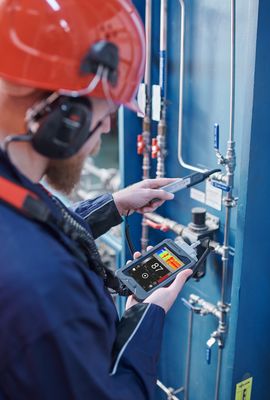
Whether it‘s large industrial companies or small businesses - Compressed air is necessary everywhere. The list of industries with compressed air supply is long. Some of the ways compressed air can be used are as an energy source, for cleaning, for painting or for the production of Nitrogen. Apikal Anlagenbau GmbH in Lauta has specialized in innovative solutions regarding compressed air technologies, system construction and special plant construction. Over 60 employees develop, plan and build compressed air systems for diverse requirements. Their customers come from all industries: the food industry to energy supply and even chemical companies. Energy efficiency plays a crucial part in planning the plants for apikal. „Many of our customers implement the energy management standard ISO 50001 systematically. We help to plan the plant in an energy- efficient manner and cover influential factors for improved energy efficiency” explains Klaus Händler, managing director of apikal Anlagenbau GmbH.
“Many of our customers implement the energy management standard ISO 50001 systematically. We help to plan the plant in an energy-efficient manner and cover influential factors for improved energy efficiency.“
Klaus Händler, apikal Anlagenbau GmbH
In addition to energy-efficient production of compressed air, apikal ensures a stable and working system of the plant. If there is a malfunction, service technicians at 9 different branches in Saxony, Saxony-Anhalt as well as Baden-Württemberg arrive within 24 hours. Thomas Müller, customer service manager from Saxony-Anhalt, is responsible for Maintenance, repairs and troubleshooting on compressed air systems for customers of apikal Anlagenbau GmbH: „Compressed air systems are still the biggest energy consumers in the industry and craftmanship. Therefore we offer our customers a comprehensive Leak Detection Package as a part of the maintenance of your systems.“ Even the most carefully planned plants have invisible problem areas. Leaks can be extraordinarily expensive. Studies show: around 30 percent of energy used for compressed air is lost through leaks.
SONAPHONE® helps with the Maintenance Work
When searching for leaks, the service technician is supported by innovative technology from the SONOTEC. The compressed air specialists have been using the SONAPHONE for some time now. With the ultrasonic testing device leakages of compressed air, gas and vacuum systems can be found in no time. Ultrasonic sound develops around leaks. Not perceptible to humans, although visible and audible with the ultrasonic testing device - regardless of flow, volume and size.
“First of all, we run a compressed air utilization analysis with our customers. That way we can find out if there are any leaks and how much compressed air is lost to it. Afterwards we use the SONAPHONE to pinpoint the leaks and to assess the loss created by them.” explains Thomas Müller. He uses the Airborne sound sensor BS10 for the leak detection.
Equipped with three different attachments the sensor can detect leakages at distances up to 8 meters away. For even greater distances, SONOTEC offers the sensor BS30. With the parabolic dish you can even track down leaks at distances of up to 25 meters.
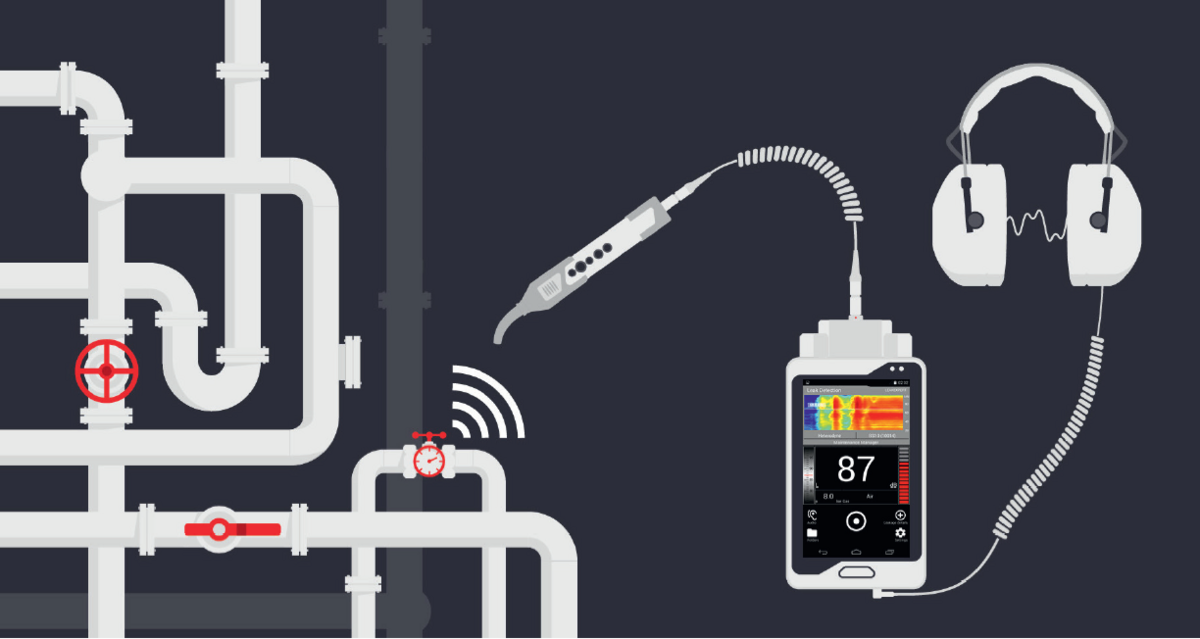
The intuitive ultrasonic testing device SONAPHONE® locates, evaluates and classifies compressed air leaks with the LeakExpert® app.
Leakage Assessment using Broadband Sensors
SONOTEC’s airborne sound sensors differentiate themselves from standard Airborne and structure-borne probes because of their broad-band range, as opposed to older narrow-band technology. A broadband microphone can process and receive ultrasonic signals simultaneosly within a range of 20 to 100 kHz. The additional information obtained is of great importance for condition assessment and paves the way for new applications, such as an automatic leakage assessment.
After the sensor has been equipped on the SONAPHONE®, Thomas Müller starts the LeakExpert® app on the device. The software is specifically tailored to leak detection and enables leak detection and evaluation while also accompanying the examiner step by step throughout the process. Thomas Müller describes the advantage of the device: „Especially the intuitive handling of the device convinced me. After a five minute instruction new employees and customers can start searching for leaks with the SONAPHONE“ System pressure and the type of gas must to be entered in the LeakExpert app to evaluate a leak and its loss.
The automatic assessment of leakages becomes child’s play.
Ambient Noise can be hidden
The service technician starts the leak detection using the gross-to-fine method. To narrow the leakage area, the large acoustic horn is placed on the airborne sound sensor. The service technician tracks the spectrogram on the display and listens to the audio through the headphones. There are two different ways to block out extraenious noise: „Phasevocoder” and „Heterodyne”. While using the audio method „Heterodyne“ a mixed frequency can be chosen to dampen ambient noise in case a high ambient ultrasonic level is expected due to ongoing processes in the plant. This makes it easy to find leaks even in demanding environments.
After the leakage area is narrowed down, the exact location of the damaged area needs to be located. For this purpose, the precise attachment is placed on the airborne sound sensor. The service technician looks for the maximum sound level and then triggers the automatic leak assessment with the push of a button.
Thomas Müller remembers the effort involved in the evaluation before purchasing the ultrasound test device: “It took a lot of experience to make a reliable estimate. We rated the leakage loss for our customers by utilizing the opening and the pressure. All of this can now be done by the SONAPHONE for us.”
After the automatic calculation of the leakage class and the loss in l / min, the service technician takes a photo of the damaged area. There is also the possibility to add voice memos and comments to the leak. More details on the location of the leak, the priority and repair instructions can also be added. The digital description of the leak is quickly created and then Mr. Müller goes looking for the next one.
Reports can be created with just a few Clicks
Thomas Müller explains what he believes to be the greatest advantage of the device: “The advantage of the SONAPHONE is especially evident at the end of the leak detection. With just a few clicks away we can create a report directly for our customers, as PDF, ZIP or CSV. Every problematic area is carefully tabulated and listed. This enables our customers to get a quick overview of where the leaks are and which are particularly critical and need to be repaired quickly.“ In the future, apikal will consider using SONAPHONE for other application areas.
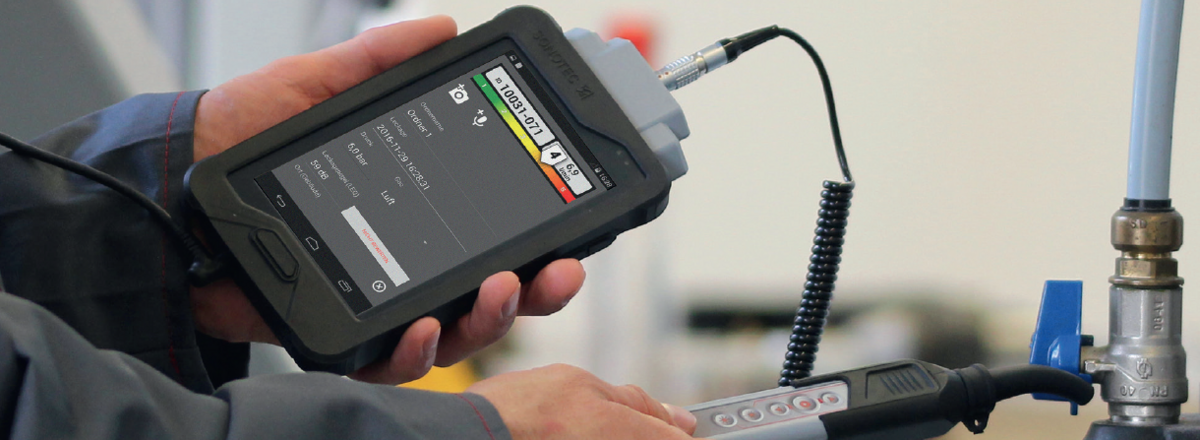
In the vicinity of the leak, the more precise sensor attachment provides information about the exact location and the amount of compressed air flowing out.
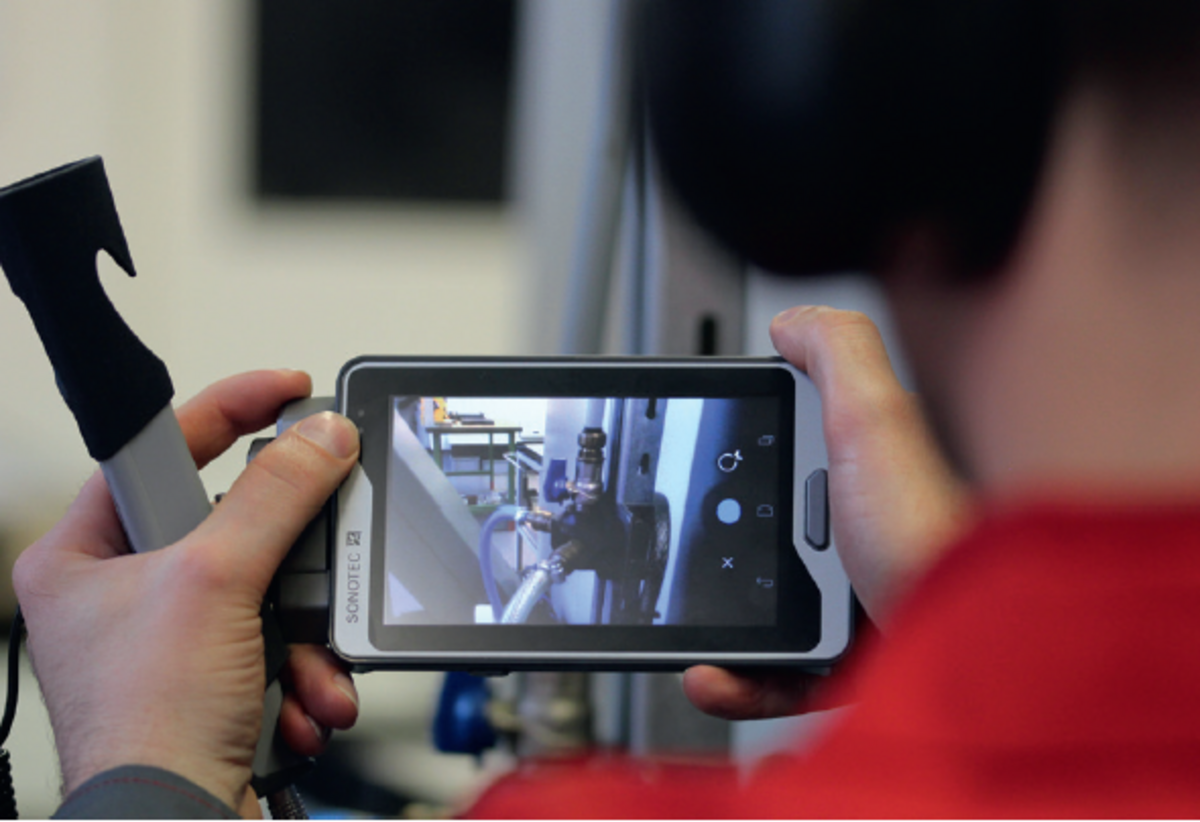
Images of the leak can be taken with the integrated camera.
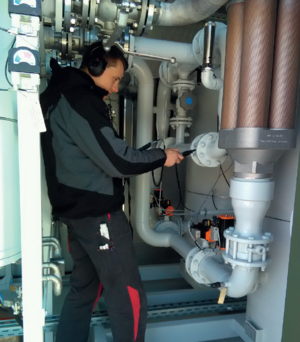
Leak test by apikal Anlagenbau GmbH after completion of the installation work on a compressed air container station
Photo: apikal Anlagenbau GmbH

By using the digital ultrasound-testing device, you can detect and assess leaks, partial discharges, the tightness of unpressurized systems as well as steam traps and bearings. The functional testing of the bearings of electric motors in compressors is particularly interesting for compressed air experts.
The broadband structure-borne noise sensor BS20 and the LevelMeter® app are used during the examination. Based on the Structure-borne noise level over time, the examiner can see how the condition of the bearing developed and take action if necessary. „By using the SONAPHONE® we save a lot of time. Our customers however, save the most important thing above all - energy. In a short amount of time you receive a report about the leaks in the plant. Appropriate repair mesures can be initiated.” Thomas Müller explains.
Both sides benefit from the new innovative technology from SONOTEC.
Do you have any questions?
Feel free to contact us! We will be happy to help you.
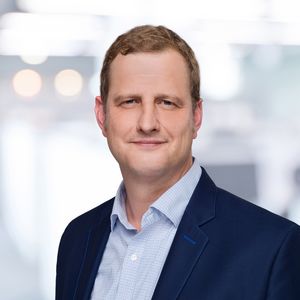