Quality Control during the Manufacture of Fiber Composite Components
How to benefit from Ultrasonic Leak Detection during the Vacuum Infusion Process
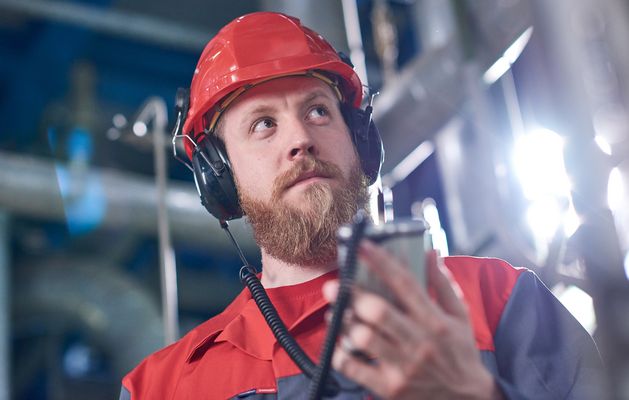
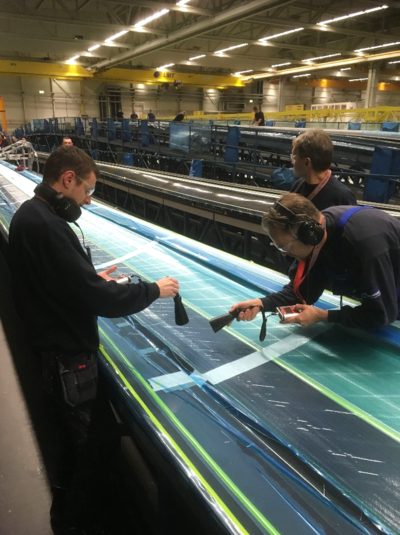
Figure 1: Leak localization using ultrasound testing technology during the filling process
Application
Composite materials are becoming increasingly important in the industrial sector due to their material properties. The manufacture of components from CFRP and GFRP often uses the vacuum infusion process. An example of a component produced on this way is the rotor blades used on wind turbines.
Modern wind turbines are being fitted with larger and larger rotor blades, in order to increase energy generation and optimize the plants. The rotor blades must be able to withstand heavy loads. This requires an efficient production process that also meets the high quality requirements.
Challenge
During the manufacture of rotor blades, the structural mold is lined with composites and reinforcement materials. In a subsequent process, the mold is sealed with film, the vacuum is applied (evacuation) and the mold is filled with resin while the vacuum is maintained. Any leaks in the film during this process can lead to structural faults. For example, any areas that are not impregnated can have a negative impact on the durability of the rotor blade.
Leaking areas create detectable noises in the ultrasonic range through the ingress of air. Therefore, using ultrasound testing technology, these leaks can be found during the filling process and be eliminated before the resin is hardened. Costly reworking or follow-up damage during operation is avoided.
Device and Attachments
- SONAPHONE Pocket Makes ultrasound
signals audible in narrow band range of 40 kHz
Digital display of the ultrasound level
- L55 parabolic probe High range and large
scanning area | Red dot sight for orientation
purposes
- L50 airborne sound probe + acoustic horn or
directional tube with tip
- Acoustic horn Detects the ultrasound source
in short distances
- Directional Tube with tip Shields against
other ultrasound sources and enables exact
localization of the leak
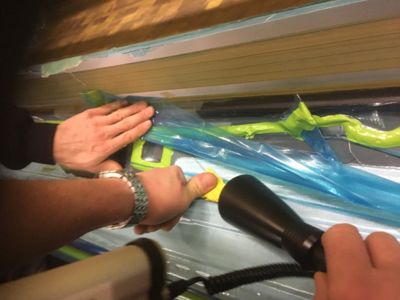
Figure 2: Sealing a leak after precise localization
Advantages
The SONAPHONE Pocket ultrasound testing devices from SONOTEC help manufacturers to detect leaks and provide:
- Quick inspection through scanning of the entire component
- Exact localization of the leak
- Prevention of non-impregnated areas and costly reworking
- Consistent component quality thanks to process optimization by means of ultrasonic leak testing
Do you have any questions?
Feel free to contact us! We will be happy to help you.
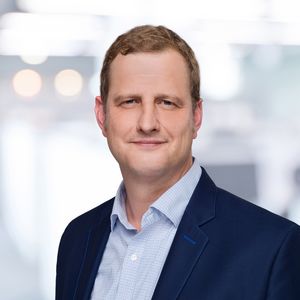