Save Energy in Steam and Condensate Systems
Germany’s oldest paper mill still in production uses digital ultrasonic testing technology to track down defective steam traps
Two apprentices at the oldest paper mill still operating in Germany received an award for their project ‘Steam traps as an important component for energy efficiency’ in a competition sponsored by the ‘Energy Transition and Climate Protection’ initiative for medium-sized companies in Saxony.
Which traps are defective and how high are the costs caused by defective steam traps? The apprentices used technology from the company SONOTEC to assist them in answering these questions. The digital ultrasonic testing device supplied them with answers, which impressed everyone.
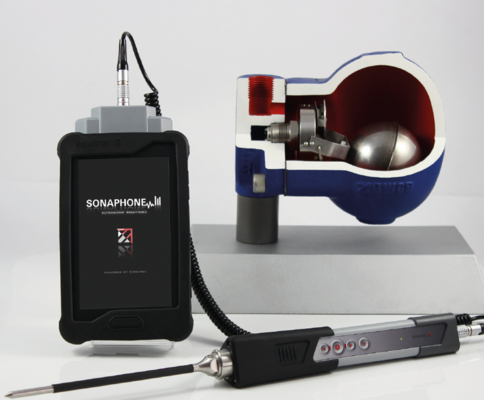
The 'Penig Paper Mill' in Saxony
Paper has been produced at Penig Papierfabrik in Saxony since 1537. Today, approximately 100 employees are employed at the oldest paper mill still operating in Germany. The mill produces décor paper under the name Schoeller Technocell GmbH & Co. KG Werk Penig, which is part of the Felix Schoeller Group in Osnabruck, Germany. Décor paper is used primarily for furniture and floors.
The machines are in operation around the clock 350 days a year and consume 110,000 MWh annually. For this reason, Schoeller is finding new ways to save energy. ‘We want to use 2 per cent less primary energy every year in relation to production volume and the base year 2012. New ideas are repeatedly needed to achieve this goal,’ says Rico Eidam, the Technical Director and Energy Manager at the paper mill.
The Apprentices are boosting the Energy Management
To achieve its energy goals, the paper mill is getting its own workforce involved. The company has been training energy scouts since 2016. Rico Eidam remarks, ‘With this qualification scheme, we want to get our apprentices enthusiastic about the topic of energy efficiency, and of course, we also want to discover new ways of saving energy’.
The apprentices Franz Weber and Martin Becher uncovered potential ways of saving energy by regularly testing steam traps. In 2018 they both were awarded a prize with their project titled ‘Steam traps as an important component in energy efficiency’.
Martin Becher, an industrial mechanic in his third year of apprenticeship, explains, ‘After we completed several modules on the topics of energy efficiency, project work and working with measuring devices at the Chamber of Industry and Commerce (IHK) in Dresden, we were given the task of implementing a practical energy efficiency project in our company.
After conducting research and consulting with the Energy Manager, the two apprentices decided to carefully examine the steam traps at the power station.
‘Defective steam traps can lead to unscheduled downtime and higher energy consumption. By regularly testing the traps, repairs and replacements can be planned better. Energy costs for steam production can also be significantly lowered, which we demonstrated in our project,’ explains Franz Weber, an electronics technician in his fourth apprenticeship year.
The paper mill primarily requires steam during the drying process, where residual water from the paper is evaporated. The décor paper web runs through the labyrinth of 30 drying cylinders in the paper machine. At the end of the process, the finished paper contains 7 to 8 percent residual moisture.
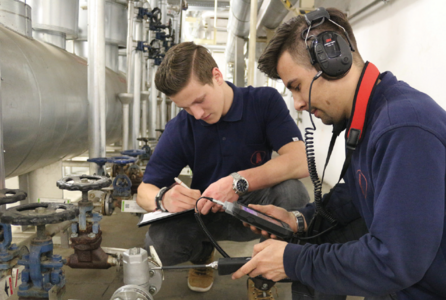
The apprentices Franz Weber (left) and Martin Becher (right) from Peniger Papierfabrik were awarded a prize for their project ‘Steam traps as an important component for energy efficiency’.
Experts assume that around 15 to 20 per cent of the steam produced is lost as a result of leaky steam traps. This calculation is an example which illustrates the costs: A leak with a diameter of only 5 mm leads to a loss of 5 bar of pressure and 65 kg of steam per hour, which means approx. 550 t are lost per year (at a rate of 8,400 operational hours annually). With production costs of €20/t , this loss can add up to nearly €11,000 per year.
Combined Ultrasonic and Temperature Testing
Martin Becher explains, ‘Up until now, we have not had much experience with steam and condensate systems. At first, we had to familiarise ourselves with the topic and we attended a one-day training session at SONOTEC.’
During the session, the two energy scouts learned, among other things, about how to distinguish between intact and defective traps using audio samples. Depending on the design, a functioning trap opens and closes continuously or discontinuously and it produces characteristic ultrasound signals during this process. They can be recorded and analysed with the digital ultrasonic testing device SONAPHONE®, the LevelMeter® App, and the broadband ultrasonic and temperature sensor BS20. The theory was then put into practice back at Penig.
A section with 28 thermal and float condensate drains were supposed to be analysed. All of the steam traps in the device were recorded and were set up as test points with an image, number and type. Then the energy scouts plugged the BS20 sensor into the device and began testing.
Initially, the temperature of the trap was measured at the inlet and outlet. The temperature can determine, for example, if the steam trap has the operating temperature expected or if it tends to be too cold (condensate backup) or too hot (leaky) depending on the system’s pressure. The difference in temperature is assessed at the inlet and outlet depending on the operating principle of the trap.
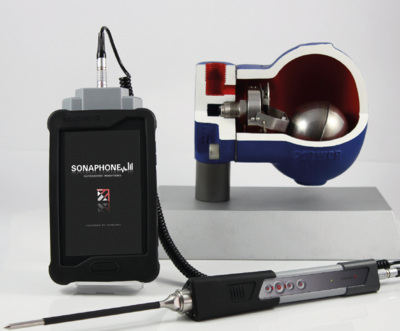
When testing the steam trap, the energy scouts used technology from the company SONOTEC to assist them. Is the steam trap working correctly or is it defective? The digital ultrasonic testing device SONAPHONE delivered the answer to this question.
The Condition Assessment requires Experience
Afterwards, the two apprentices recorded the ultrasonic signal with a broadband structure-borne sound sensor using a frequency range of 20 to 100 kilohertz. There were no problems during testing and it was also possible to conduct the tests while the equipment was in operation. They selected the measuring intervals in such a way that the steam trap had circulated and drained at least once.
An interval of approximately one minute was used for the float condensate drain and an interval of about three minutes was used for the thermal drain. The emission of an acoustic signal on the display in the form of a spectrogram proved to be helpful for their subsequent evaluation.
The characteristic sound changes of defective steam traps can be distinguished immediately from the characteristic sounds of intact traps.
‘Initially, we recorded the signal from a new trap which was very likely working properly. Then we were able to compare the recording with the other recordings and could draw some conclusions about which traps were defective. This also involves having a little experience.’
Franz Weber, Schoeller Technocell GmbH & Co. KG Werk Penig
During the testing process, the two apprentices used the LevelMeter® App. After recording temperature and ultrasound, they could add photos, voice memos and comments on each test point. Franz Weber says, ‘Handling the SONAPHONE® is really very intuitive and easy; it is similar to using a smartphone. Once we were finished, we could create a report with just a few clicks.’
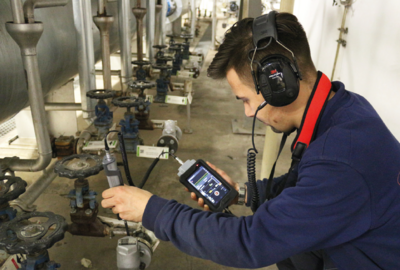
Temperature measurement with a combined structure-borne sound and temperature sensor BS20
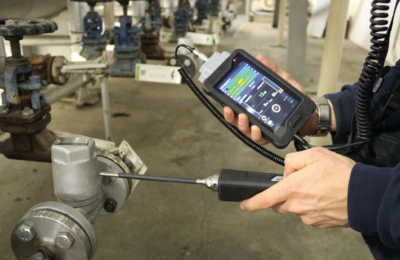
Recording the ultrasonic signal at a frequency range of 20 to 100 kilohertz with a broadband structure-borne sound sensor. The characteristic sound changes of defective steam traps can be distinguished immediately from the characteristic sounds of intact traps.
50 Percent of the Traps were defective
At the end of the case study, everyone was surprised about the results of the tests. Fifty percent, i.e. 14 of the 28 traps, proved to be defective.
Rico Eidam states, ‘If we assume that one defective trap costs us about 4,000 euros per year, we can save around 48,000 euros alone in this section by replacing the traps.’ The last defective traps will be replaced during the next downtime. The Energy Manager reports, ‘The temperature of the condensate has dropped considerably since we changed the first traps.’
In the future, all of the steam traps in Peniger’s factory will be recorded and tested on a regular basis. The scheduled preventive maintenance will include monitoring the condition of the traps every six months. Moreover, the team also plans to use the SONAPHONE for other maintenance tasks.
For example, they can use the digital testing device to detect leakages in the compressed air systems and to monitor the condition of roller and ball bearings. Additionally, the testing device is suitable for inspecting partial discharges in electrical equipment. When it comes to saving energy, Peniger has taken the lead.
The energy scouts received an award for their project ‘Steam traps as an important component for energy efficiency’ in a competition sponsored by the ‘Energy Transition and Climate Protection’ initiative for medium-sized companies in Saxony. ‘We, of course, are proud of this achievement. Up until now, we have been able to exceed our goal for saving energy every year. This type of project is an important component for achieving our goal and it raises the awareness of this issue among all our staff.'
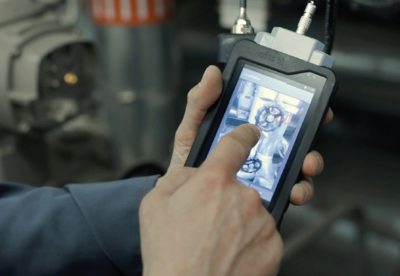
After the temperature is taken and the ultrasound is recorded, photos, voice memos and comments on each test point can be added.
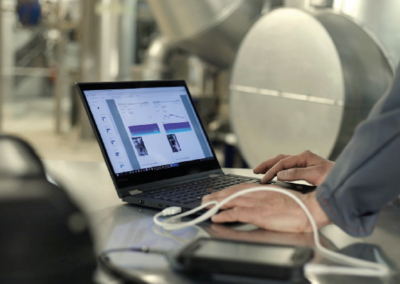
An evaluation of the steam trap can be conducted on site or later at your computer using DataViewer software. The report can be exported as a CSV or PDF file for documentation purposes.
Do you have any questions?
Feel free to contact us! We will be happy to help you.
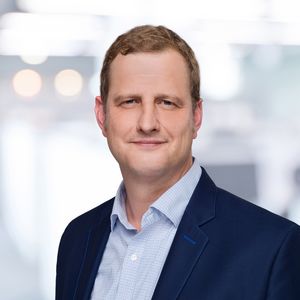