FAQ-L.3: What tightness requirements (leak rate) can be fulfilled using ultrasound testing with air-borne sensors in standard industrial environments?
There is a variety of applications and suitable methods to find and assess leakages. Acoustic testing with air-borne sensors is used when leaks are to be found relatively quickly and without great technical effort. Pressure differences cause air to leak from the system (overpressure) or into a vacuum system (underpressure). Starting at certain leak sizes turbulent flow is created, which in turn is responsible for the generation of ultrasound.
However, the detectable leak rate using air-borne sensors is limited by physics and the performance of available electronic components. On the one hand, several factors determine if and to what extent a turbulent flow is created. As example, due to physical characteristics a turbulent flow only arises above a leak rate of 10⁻² mbar l/s. Furthermore, a pressure difference of approx. 500 mbar between the system and the environment is needed. On the other hand, the electronic components used in ultrasound instruments constrain the lower measuring scale. Economically reasonable sensor technology limits the signal to noise ratio and thus the system’s sensitivity.
The above-mentioned reasons are mainly responsible that tightness requirements of 10⁻² mbar l/s or "watertight" cannot be reliably and reproducibly met in industrial environments using standard ultrasound technology!
However, there are applications where locating and evaluating leaks with less demanding requirements is relevant, e.g. in the field of energy efficiency in compressed air and steam systems as well as in leak testing using ultrasound transmitters (e.g. in transport and shipbuilding). In the field of quality assurance, requirements need to be defined and approved by the customer in order to get a qualitative assessment of components and subassemblies.
Do you have any questions?
Feel free to contact us! We will be happy to help you.
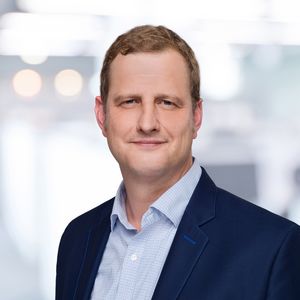