Ultrasonic Testing Devices
For Preventive Maintenance
Optimizing processes, increasing operational reliability and improving energy efficiency are becoming more important than ever. Our ultrasonic testing devices enable fast and reliable testing of equipment and preventing failures - whether for detecting leaks or defects in rotating components, monitor lubrication, test steam traps or for electrical inspections.
✓ Applications, demo and pricing
- Detect leakages, monitor the condition of machines, inspect electrical systems, test tightness and more
- Save costs and increase efficiency
- Broadband sensor technology for high frequency ultrasonic testing
- Record and document your findings with our tailored web and app concept
Bring your maintenance strategy to the next level with our SONAPHONE® product range.
Advantages at a Glance
Upgrade your preventive maintenance processes with our ultrasonic testing devices
Multiple Maintenance Applications Using Ultrasound Technology
Ultrasound technology and our solutions
One of the main advantages of using ultrasound is the early detection of defective areas by making ultrasonic sound emissions audible. The detection at the earliest stage is crucial for eliminating problems before they develop into major failures or safety risks.
Digital Device & Software
The SONAPHONE Web & App concept features intuitive apps and Software tailored to specific preventive maintenance applications. Process-related documentation can be carried out directly on the device. Apps accompany you through the entire testing process: from planning, testing and documentation to analysis via touchscreen and relevant information can thus be bundled.
Innovative Broadband Sensors
Various airborne and structure-borne sound sensors are available for a wide range of applications, making SONAPHONE devices versatile tools for a successful maintenance strategy. The development and construction of our sensors is carried out in-house, ensuring their high quality and accuracy.
FAQ
Compared to other technologies, ultrasonic testing devices allow the earliest possible detection of damages, long before they result in a downtime or system failure. Defects such as gas leaks, worn bearings or partial discharges most often generate ultrasonic sounds that are inaudible to humans. For example, small leaks create turbulences that are not audible before they get bigger, and a bearing's frequency changes before it cracks. Simply put, your equipment is talking to you long before failing, but you cannot hear it. This is where our SONAPHONE devices come to your help: They detect the ultrasonic sound emissions of leaks, failing bearings or partial electrical discharges and let you hear them, so that you can identify and repair the concerned components. Thus, implementing a preventive maintenance strategy using ultrasound gives you time to order needed parts, plan and execute repairs without being surprised by unexpected downtimes or costly system inefficiencies.
The use of ultrasound in preventive maintenance delivers reliable results even in the presence of industrial noise. Our ultrasonic detectors operate in the frequency range above 20 kHz, which is beyond the range of human hearing. In noisy industrial environments, this frequency range is less affected by typical industrial background noise, as most industrial noise is in the low-frequency range below 20 kHz. So what for humans is loud industrial noise does not impact our devices.
The earliest sound signals generated by defects are in the ultrasonic range - our sensors are designed precisely for these frequencies. Many ultrasonic measurements, for example in the field of bearing inspection, are also carried out by direct physical contact with the object to be examined, which further minimizes the influence of surrounding noise.
Do you have any questions?
Feel free to contact us! We will be happy to help you.
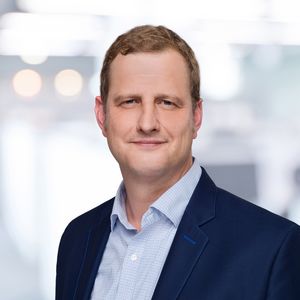